Date: Spring 2017
Collaborator: David Franck
Critics: Duks Koschitz, Chei Wei Wong
Honors:
Interviewed and featured in Prattfolio Spring/Summer 2018 Magazine
Project selected for the Distinguished Projects 401 Review in the Fall 2016 Semester as one of five out of over 140 students
Project archived as best of studio and displayed in InProcess Magazine
This project questions and explore the role of tools in the design practices. More often then not speculative projects in studio settings take on specific characteristics based on the software and techniques used to create them. To break out of this paradigm we created a tool that would become our "third partner" to design with. Through this investigation we were able to discover novel manufacturing processes of our own as well as the fundamentals of engineering a machine.
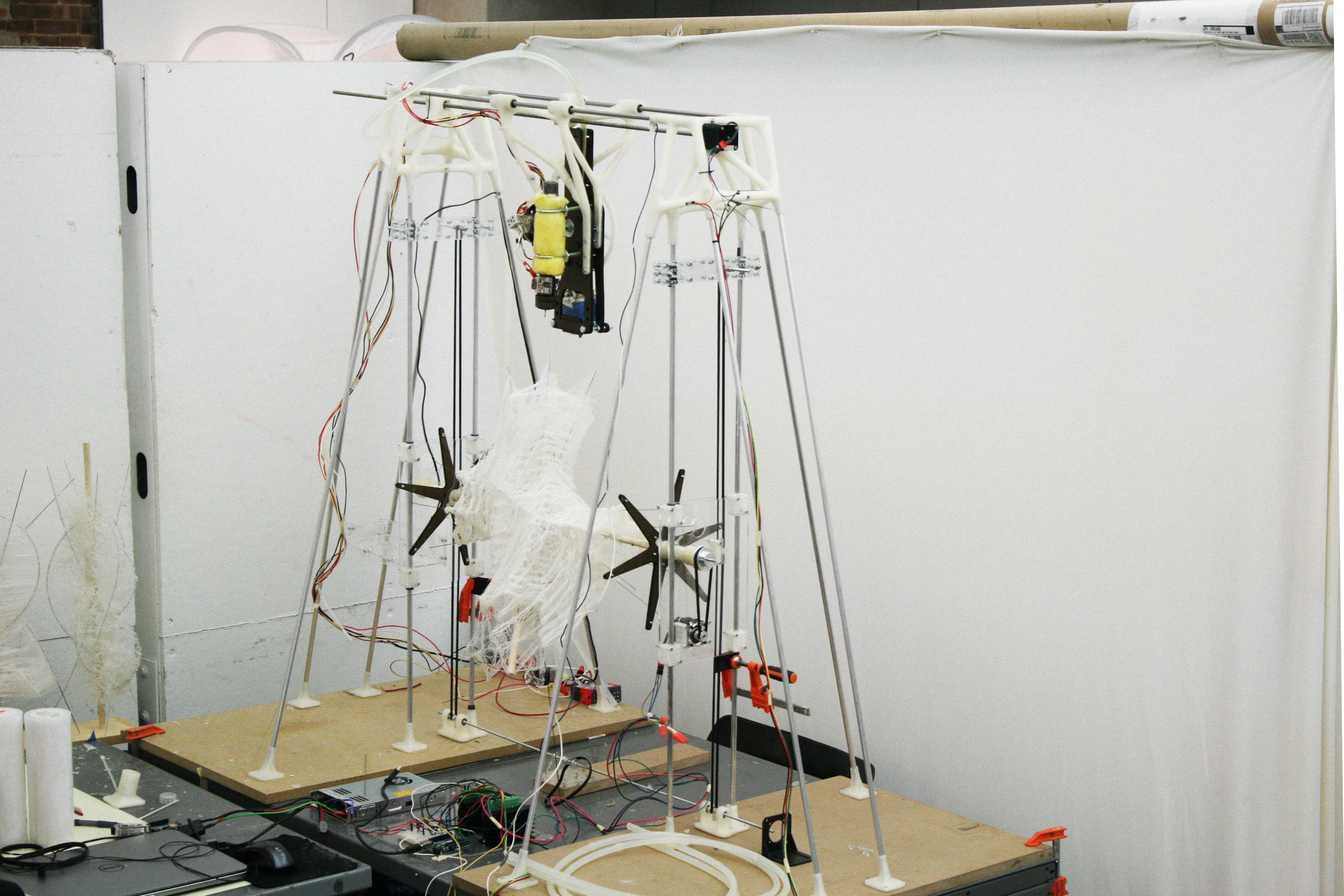
The Machine
The tool we built made use of a rotational axis which held a frame or substrate, and a linear axis with a custom extruder. Both axis were programmed to work together to create a cocoon form. To explore form making in this way we would vary the patterns, speeds, extruded materials, and substrates.



The Artifacts
Some Examples of the artifacts that were able to produce through our novel manufacturing process. One of our big discoveries was that there was another scale of fidelity that could be achieved through an understanding of material behavior.



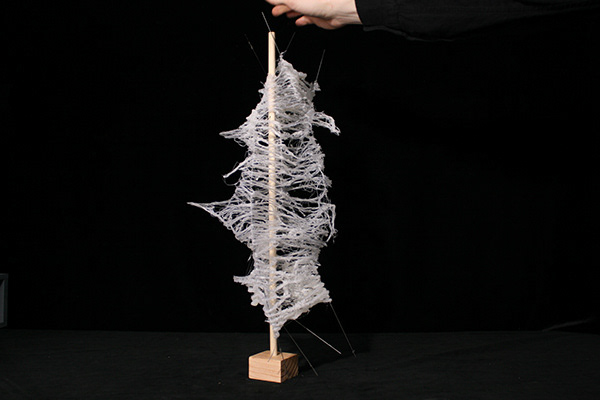


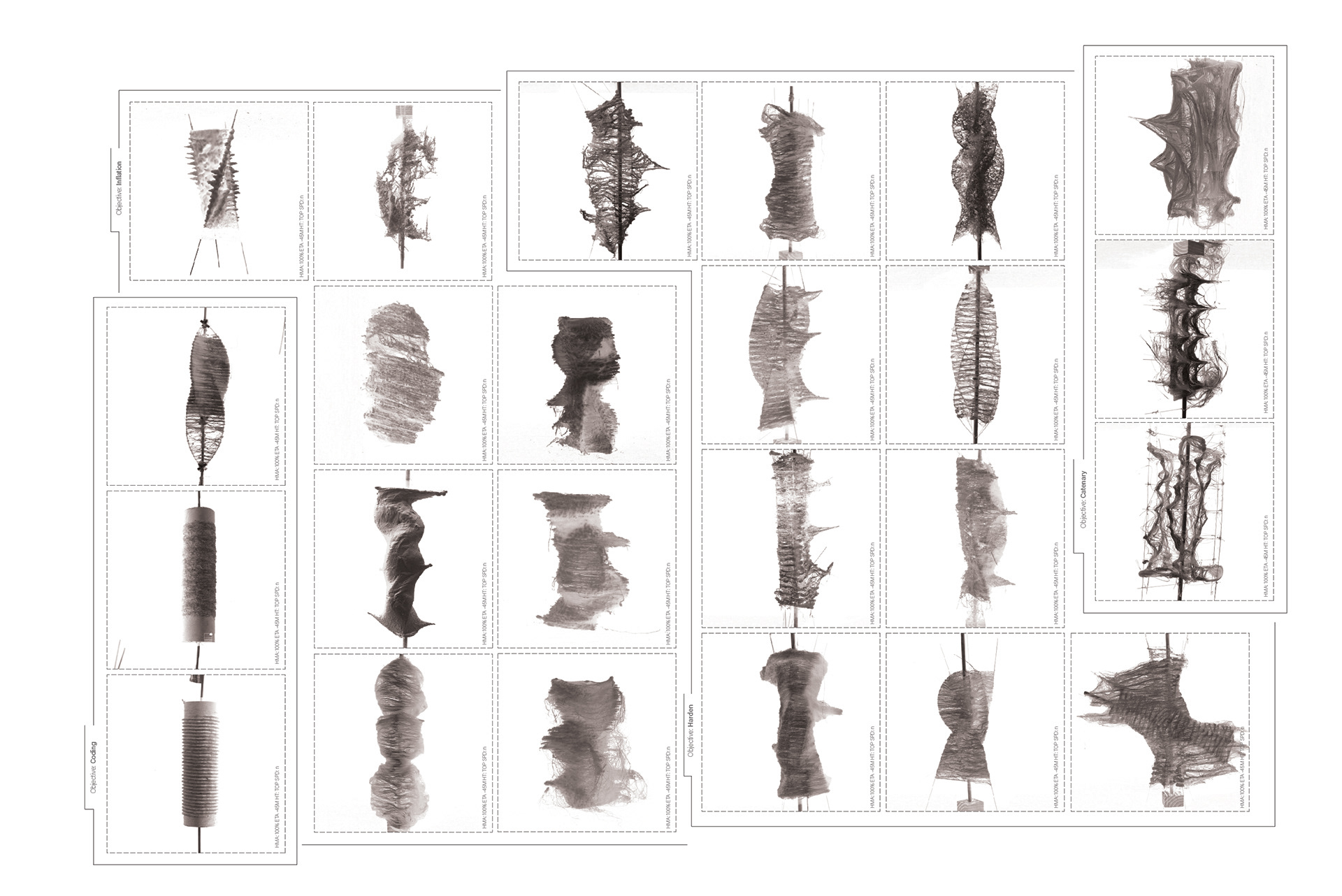
Matrix of Artifacts produced from 2 Axis Lathe Extruder
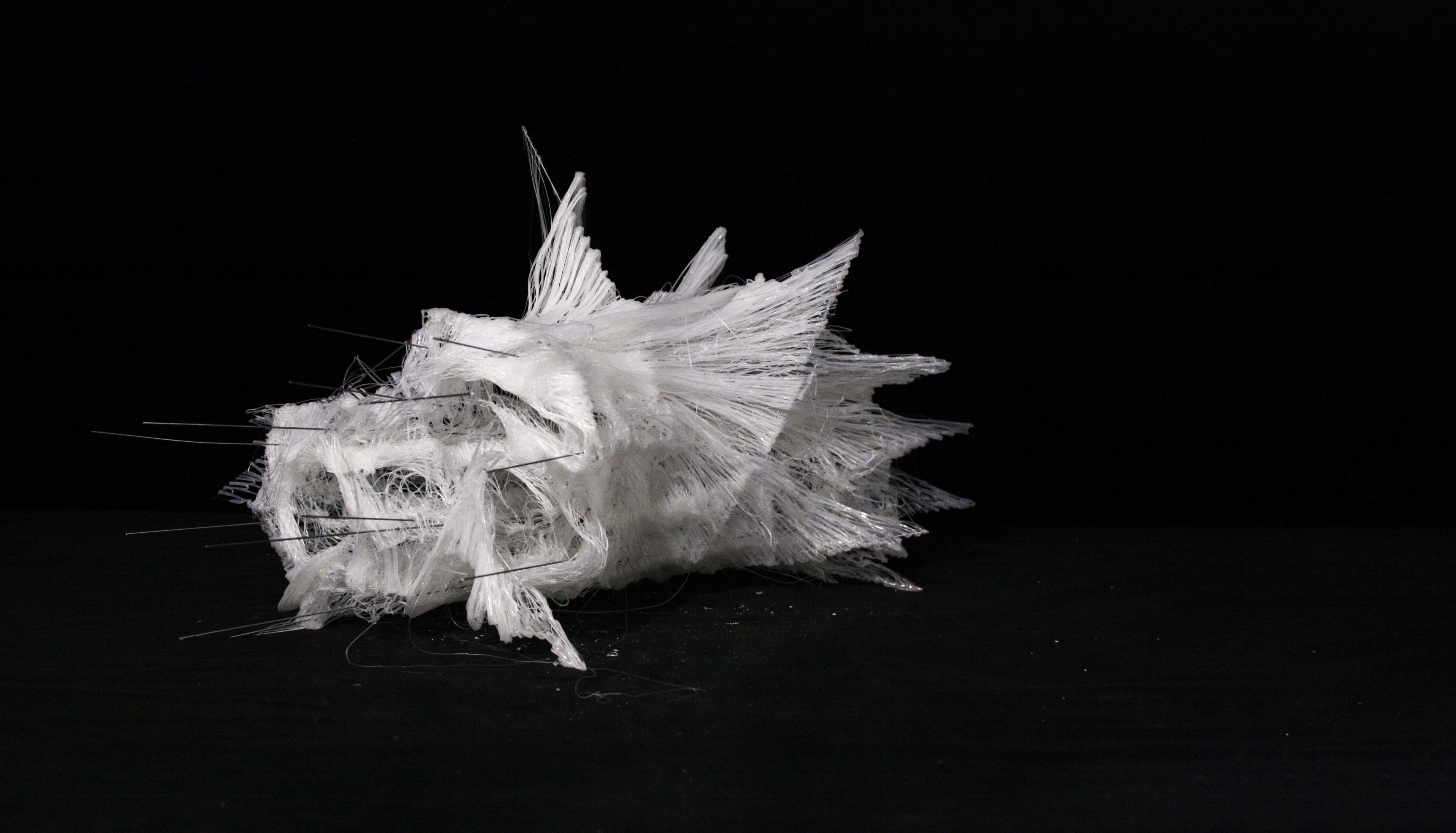
Final Artifact 12X24” HMA, Spring Steel
Deployed Artifact to Architecture
To create an architectural proposition we imagined a reality in which our machine was deployed at a large scale to space between two buildings, creating a floating environment anchored to its surroundings. The spatial complexity achieved through the intersection of two axes.
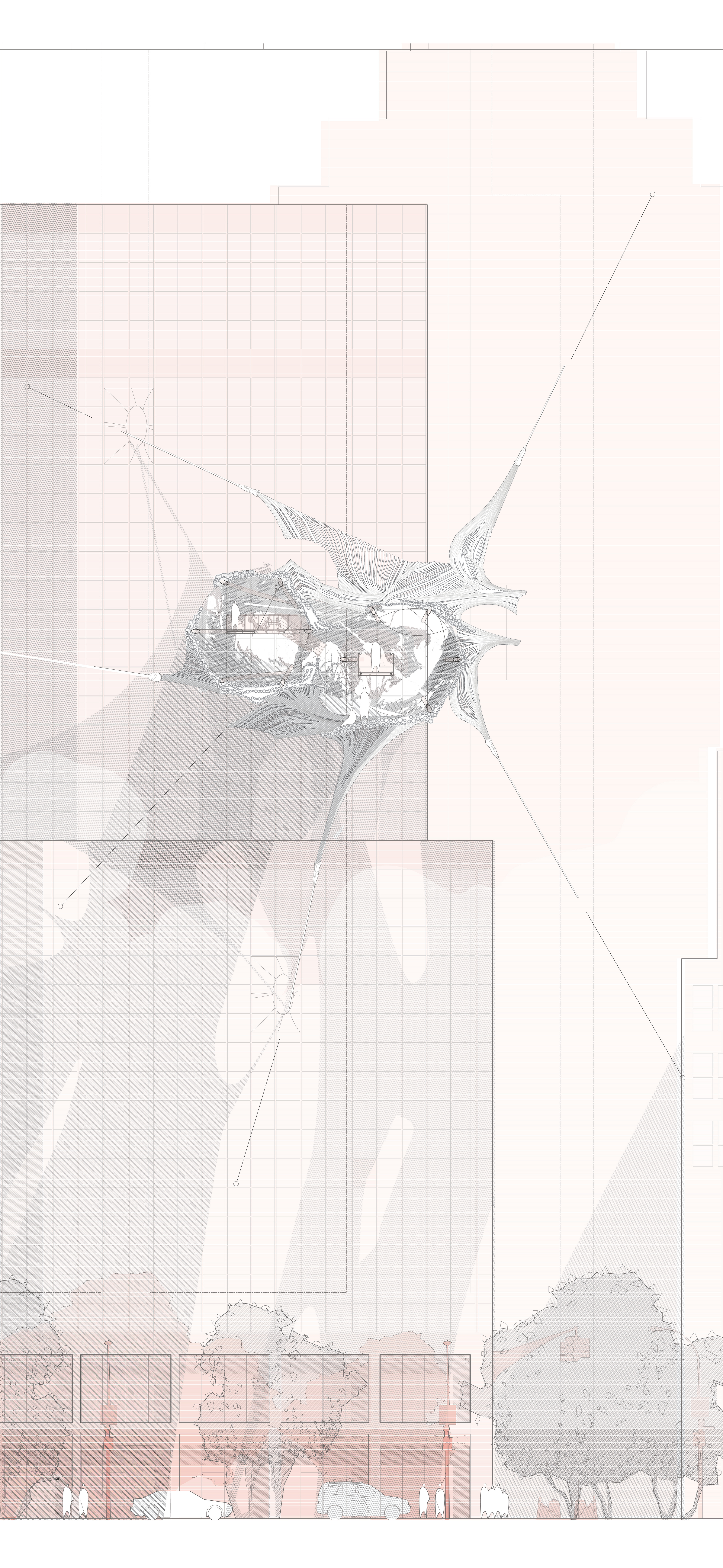
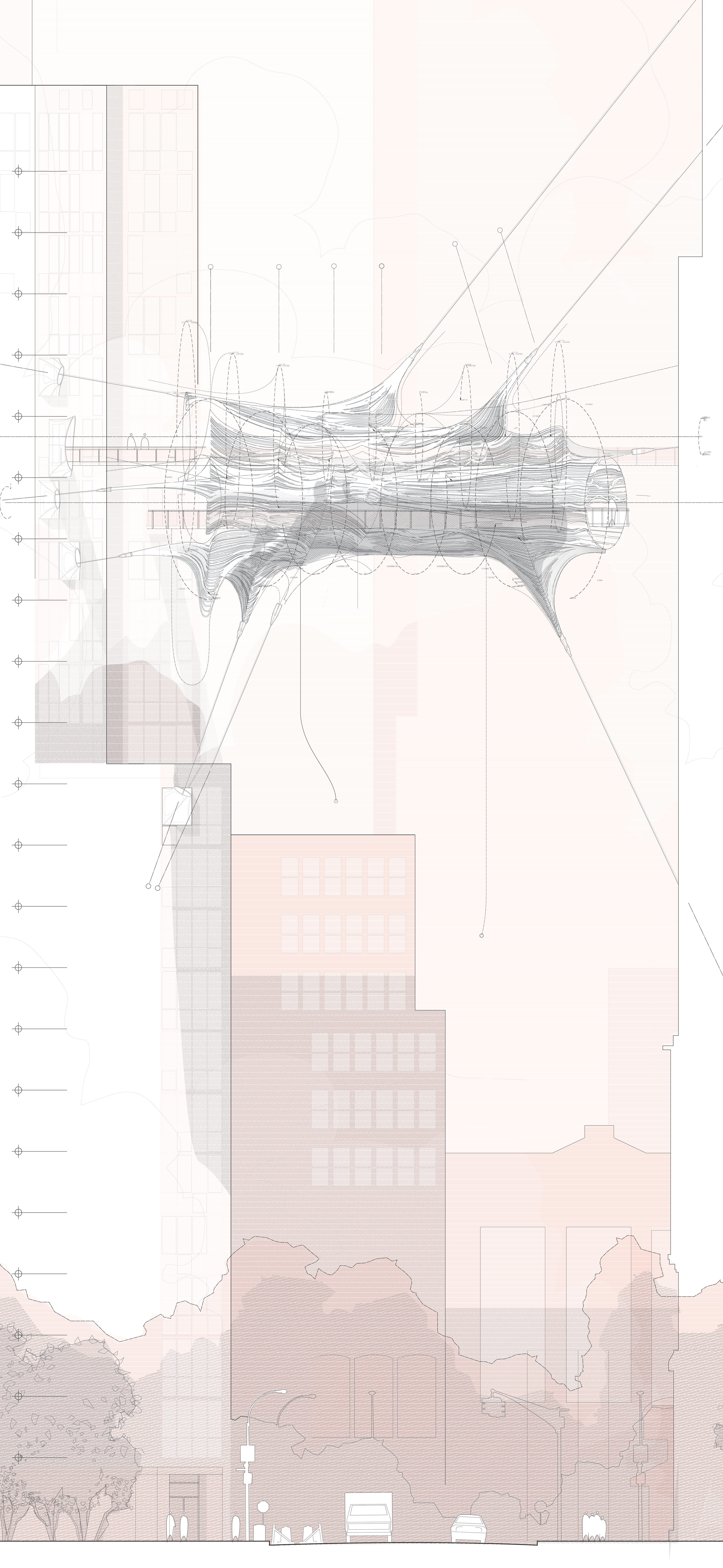